Polymer coating of Metal
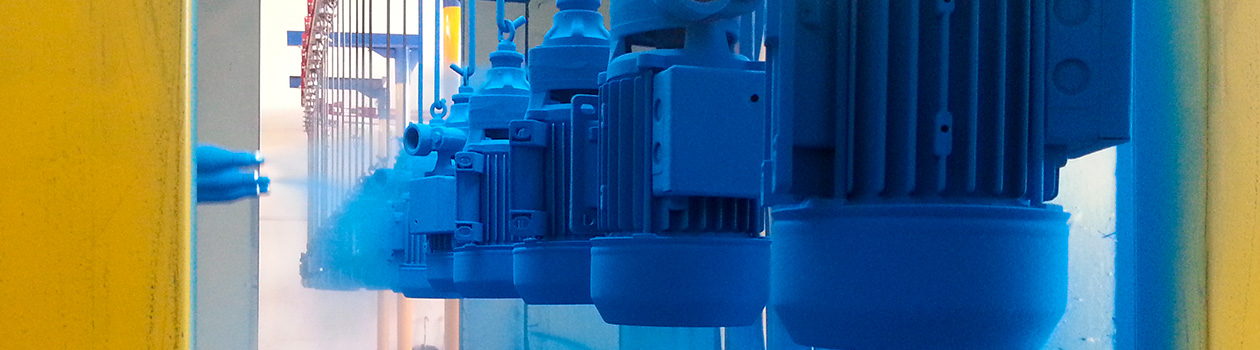
Polymer coating of Metal - the method of painting involves applying a sintered polymer dye to the metal surface. Such metal processing makes it possible to obtain a durable protective and decorative coating.
Polymer painting is carried out using specialized equipment of various types, depending on the amount of painting work and the characteristics of staining. Most often, the following types of equipment are used for this purpose:
- Special painting booth where most of the entire painting process takes place. Its design consists of a frame and metal sheathing. In the chamber, due to air purification, the powder dye that has not fallen on the surface to be treated is sent to the filters, and then dumped into a container, which allows it to be reused;
- spray gun - a device that allows the use of compressed air, without which it is impossible to perform powder coating. This tool, depending on the size, is manual or industrial;
- an oven for "sintering" the coating formed as a result of polymer painting;
- Chamber for sandblasting the surface to be painted, in which, due to the action of abrasive particles under pressure, everything superfluous is quickly removed.
Technology
Polymer painting technology Powder painting involves the phased execution of painting work in the following sequence:
- The metal blank is cleaned of dust and dirt, traces of rust and oxides are removed from the metal, its surface is degreased.
- All dents are leveled and the workpiece is allowed to dry completely.
- The cleaned and dry workpiece is placed in the chamber to be painted, where the polymer powder coating is applied using a suitable spray gun.
- The billet is moved into the coating curing oven at a certain temperature. Due to uniform heating, the formation of a single polymer film is ensured.
- The painted product is sent for cooling.
Depending on the operating conditions of the product, various paints and varnishes are applied after powder coating.
Benefits
Polymer painting has a lot of advantages over traditional methods of applying a protective and decorative coating, which include:
- maximum adhesion to the metal surface;
- high resistance to various kinds of influences (atmospheric, aggressive environments, physical);
- reliable protection against rust;
- the speed of painting, after which it is not necessary to wait for the surface to dry, and the product can be immediately sent to operation;
- environmental compatibility of the coating is guaranteed by the absence of any odors;
- color fastness to fading;
- decorative appearance;
- This method of applying the dye increases the service life of the coating (up to 20 years or more).
Result of work
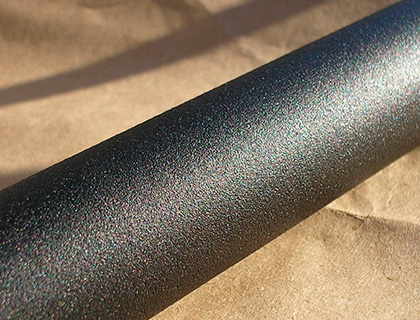
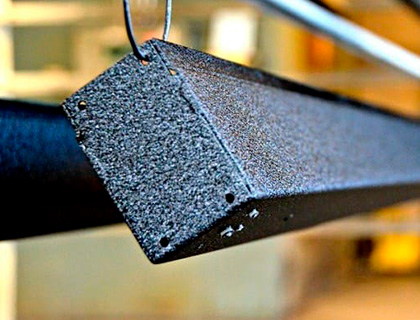
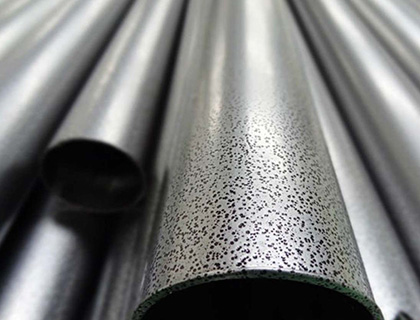
As a result of polymer painting, a durable coating is created, which is distinguished by excellent electrical insulating and anti-corrosion properties, as well as resistance to various substances. Coating a metal surface with polymeric compositions has many advantages over painting it with enamel paints and varnishes. An extensive range of colors allows you to give the product a beautiful appearance. Powder dyes after sintering form a layer having a single structure with good adhesion to the base. This provides wear resistance and durability of the coating.
The basis for metal-layers are sheets of steel or aluminum, so this structural material is especially durable. If we compare the base metals of metal-layers, then we must keep in mind that steel is three times stronger than aluminum alloy, so the load-bearing capacity of metal-layers with a steel base is much higher. Temperature line coefficient The expansion of aluminum is twice that of steel, but the modulus of elasticity of aluminum is three times less than that of steel. Aluminum sheets are much lighter and have a smoother surface. This material is more resistant to acidic environments than steel.
Metal-plastics, regardless of the base material, are coated with zinc by immersion in a metal that is in a molten state. To form a protective coating, galvanizing is also used. For metal-plastics, zinc coating is considered the most reliable and durable.
Among the requirements for coatings made of polymer dyes for metal-plastics, one can single out the use of plastic that is resistant to impact loads and abrasion. The choice of the type of plastic depends on the environmental conditions in which the structural material will be used. The use of non-resistant plastic leads to aging of the polymer paint. This state of polymers causes an irreversible change in their electrical insulating and anticorrosion properties. Aging often causes that the polymer changes color: fades, fades, fades in the sun.
In the process of manufacturing a metal-plastic, it is important not only to choose a certain type of polymer, but also to use the material necessary for the finishing coating. For this purpose, such types of materials as organosol, plastisol, film and powder coating are suitable.
Plastisols are dispersions of polyvinyl chloride, pigments and fillers in plasticizers with the addition of modifiers and stabilizers. This composition has good decorative qualities. Plastisol is applied by spraying. Due to the large layer thickness (175 and 200 microns), metal-plastics coated with plastisol are considered the most resistant to mechanical damage. Polyvinyl chloride is sufficiently resistant to aggressive environments.
Organosols are in many ways similar to plastisols, but along with plasticizers, they contain volatile organic solvents that reduce viscosity and improve coating spreadability. Due to the small thickness (30-50 microns) of the organosol layer, it turns out to be more solid. Volatile dispersants in the composition of the organosol accelerate the swelling of polyvinyl chloride.
The surface painted with powder dyes is covered with a film in order to improve the decorative qualities. Films are used in different (50-500 microns) thickness. This polymer paint protection method is suitable for indoor products.
In addition to the listed materials, substances in the form of powders are used to protect the polymer coating. The advantage of such a protective and decorative layer is the possibility of uniform application without cracks and porous areas.